If you’re in the business of explosion-proof products, you’ve likely encountered a series of cryptic markings on these items. Ex d, Ex i, Ex e, Ex mb – it can feel like decoding a secret language. You might find yourself pondering, “Which product is right for my application, and what sets these markings apart?”
Let’s embark on a journey to demystify these enigmatic labels. By the time you finish this article, you’ll be well-versed in the world of explosion-proof solutions, leaving behind any lingering confusion.
Table of Contents
Introduction
In hazardous areas, different types of protection methods are used to eliminate or significantly reduce the risk of explosions. As per IECEx 60079 these protection methods are defined. We will see each methods and their techniques.
Basically there are four major protection techniques:
1. To contain an ignition from escaping outside the equipment
2. To prevent a potential ignition
3. To limit the ignition energy of the equipment
4. To prevent the explosive atmosphere from contacting the ignition sources
Let’s explore each methods one by one:
Types of Protection Methods
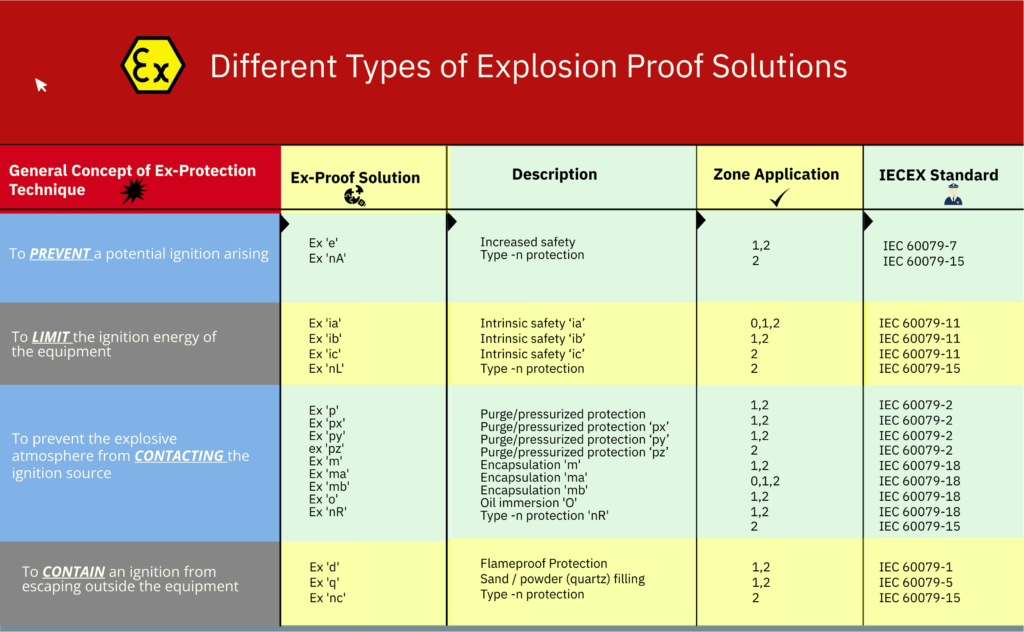
Exd – “Flameproof Enclosures”
Flameproof-proof enclosures are the backbone of explosion protection. These robust enclosures are constructed to contain any internal explosion and prevent it from igniting the surrounding hazardous atmosphere. They are used to house electrical components like switches, control panels, or lighting fixtures. Flameproof enclosures are built to withstand high-pressure conditions and have tightly sealed joints, making them an essential safeguard in industries such as petrochemical, mining, and manufacturing.
Ex i – “Intrinsically Safe Equipment”
Intrinsically safe equipment operates on the principle of safety through low-energy levels. It is designed to limit electrical and thermal energy to prevent the initiation of sparks or heat that could trigger an explosion. Common intrinsically safe equipment includes smartphones, tablets, and sensors. These devices are commonly used in locations where flammable gases or dust pose a risk, such as oil refineries, chemical plants, and grain mills.
Ex e – “Increased Safety Protection”
Increased safety, or “Ex e,” protection focuses on preventing sparks and excessive temperatures within the equipment. Ex e protection achieves safety by ensuring that the equipment is securely connected and that electrical circuits are protected from damage. This method is common in industries that require frequent maintenance or equipment access. Its emphasis on secure connections reduces the risk of sparks caused by loose components.
Ex n – “Non-Incendive Protection”
Non-incendive, or “Ex n,” protection is an economical alternative for areas where hazardous gases or dust are less likely to be present. It is designed to prevent electrical equipment from producing sparks or thermal effects that could ignite the surrounding atmosphere. This method is often applied in environments where the risk of explosion is relatively low, like water treatment plants or food processing facilities.
Ex p – “Purging and Pressurization Systems”
Purging and pressurization systems maintain a clean and controlled environment within electrical enclosures. They operate by replacing the hazardous atmosphere inside the enclosure with a clean and non-hazardous one. Purging systems push clean air or inert gases into the enclosure, while pressurization systems maintain a positive pressure to prevent hazardous gases from entering. These methods are typically used in Class I, Division 2 hazardous locations and are effective in environments where explosive gases are occasionally present.
Ex m – “Encapsulation”
Encapsulation involves completely sealing electrical components to ensure that they cannot produce sparks or heat. This method encapsulates the components within a resin or compound that is impervious to the hazardous environment. Encapsulation is a common choice for simple electronic devices or sensors used in areas where flammable gases or dust are present.